the frame
Jig / Frame is used to locate the bulkheads and provide support whilst the hull is planked.
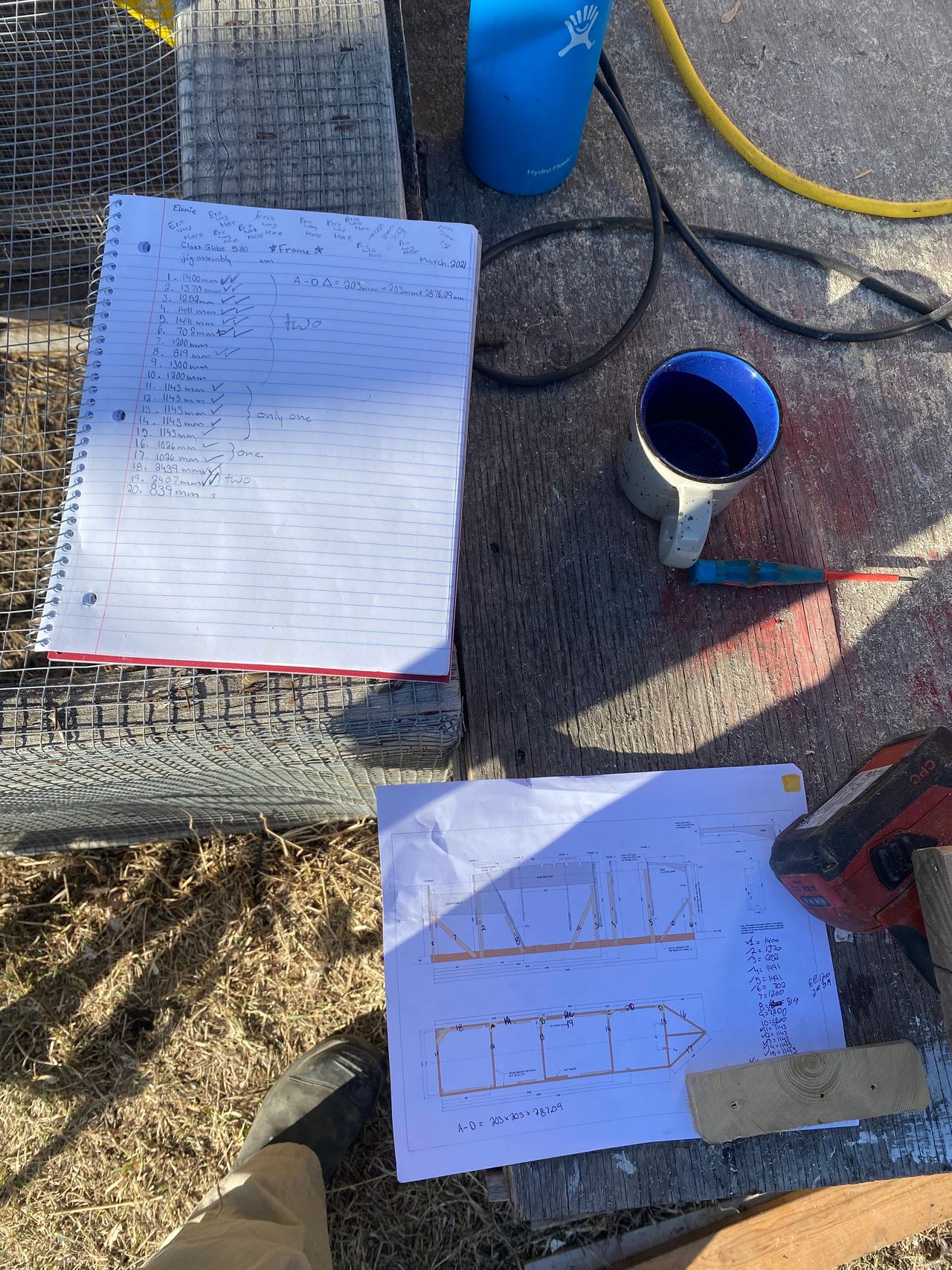
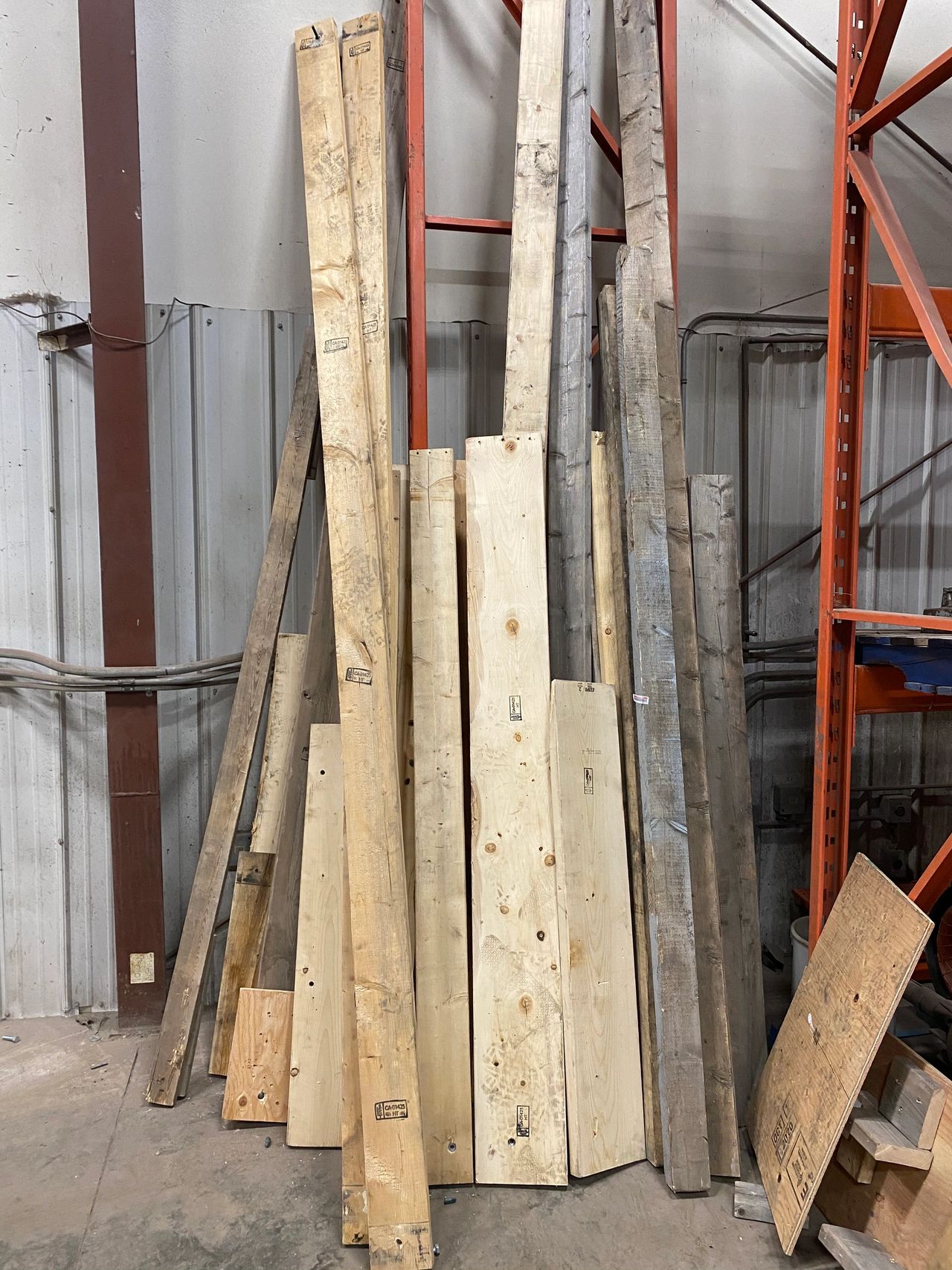
21/Nov/2021
Base of strong back and most of the uprights set up squared, levelled and elevation set.
My shop floor is not level and the scrap lumber I used would cover all the defects you’d find in the picked over lumber pile at any hardware store. So instead of relying on the elevation from the base of the jig as per the drawing, I have set up a laser level on the Center line of the boat and about 150mm above the finished hull level. I have landmarked it vertical and horizontal in several places on the building and made a fixed bracket so I can’t reset it if required or transfer to a different location and maintain the same elevation.
I have bolted the strong back to the shop floor with thread rod so I could adjust square and used chocks near the mid line of the boat to straighten the long rails.
I have levelled the strong back to with in a mm from bow to stern and port to starboard.
I double checked the Center line with a string line and all looks good.
Placing the steam support is probably the next challenge, it’s not vertical.
I hope with the work to set this it will give me a good foundation to hang the frames, which will need to be set for location and elevation as well as the vertical 2x6 that supports them is another variable.
Review.
I should not have used the low quality lumber I did. It warped, twisted and cupped. This meant when i hung the transom it was 5mm out, which required removing all the frames up to frame D and reseting them.